1DCAEとは
1DCAEに関する背景、概要、事例等を紹介します。
1DCAEの背景
ものづくりは概念設計に始まり、機能設計、配置設計、構造設計、製造設計と進みます。しかしながら、設計の初期段階では設計情報があいまいなため、CAD/CAE等の設計支援ツールを適用することが困難です。設計の後半段階になるとCAD/CAEが適用可能となりますが、この段階では多くの設計制約があり、自由に設計することが困難となります。また、設計の後半にはCAD/CAEだけでなく実体設計RP(Rapid Prototyping)や実験も可能となります。従って、設計の上流段階から適用可能な設計の考え方、設計支援ツールが望まれています。
成熟した産業分野においては配置設計、構造設計を起点にしたものづくりでも十分な効果が期待できますが、顧客の多様な要求に迅速に対応しないと乗り遅れてしまう産業分野(最近の日本ものづくりはここが弱いと言われている)においては、ものづくりの起点を設計の上流である概念設計、機能設計に置くことが強く求められています。
そこで、上流段階から適用可能な設計支援の考え方、手法、ツールとして1DCAEを提案しています。1Dは特に一次元であることを意味しているわけではなく、物事の本質を的確に捉え、見通しの良い形式でシンプルに表現することを意味します。1DCAEにより、設計の上流から下流までCAEで評価可能となります。ここで言うCAEはいわゆるシミュレーションだけでなく、本来のComputer-Aided Engineering を意味します。
1DCAEでは、製品設計を行うに当たって(形を作る前に)機能ベースで対象とする製品(システム)全体を表現し、評価解析可能とすることにより、製品開発上流段階での全体適正設計を可能とします。全体適正設計を受けて(この結果を入力として)個別設計を実施、個別設計の結果を全体適正設計に戻しシステム検証を行います。
1DCAEでは製品開発目標を設定、これに則って概念設計、機能設計を行う。製品の機能を考えることにより、設計仕様を仮決定し、3D-CAE部分に受け渡します。3D-CAEでは1DCAEから受取った仕様に基づいて構造設計、配置設計を行います。3D-CAEはいわゆる構造を考える部分であり、従来のCAD/CAEが威力を発揮します。3D-CAEの結果は1DCAEに戻され、システムとしての機能検証を行います。広義の1DCAEとはこの1DCAEを起点とした3D-CAEも含む設計の枠組みである。
1DCAEは対象とする製品の価値、機能、現象をハード、ソフトに関わらずもれなく記述し、パラメータサーベイを可能とする環境を構築します。目的に応じて、製品を使用する消費者、社会、経済、流通といった非物理現象(実はこちらの方が製品開発にとっては重要)も含む場合があります。
また、1DCAEと3D-CAEの関係は車(自転車)の両輪と考えることもできます。1DCAEにより目標設定を正しく行うための方向付けを行い、3D-CAEにより目標に向かって加速することにより、全体として高い目標を設定でき、かつ、最短でゴールすることを可能とします。
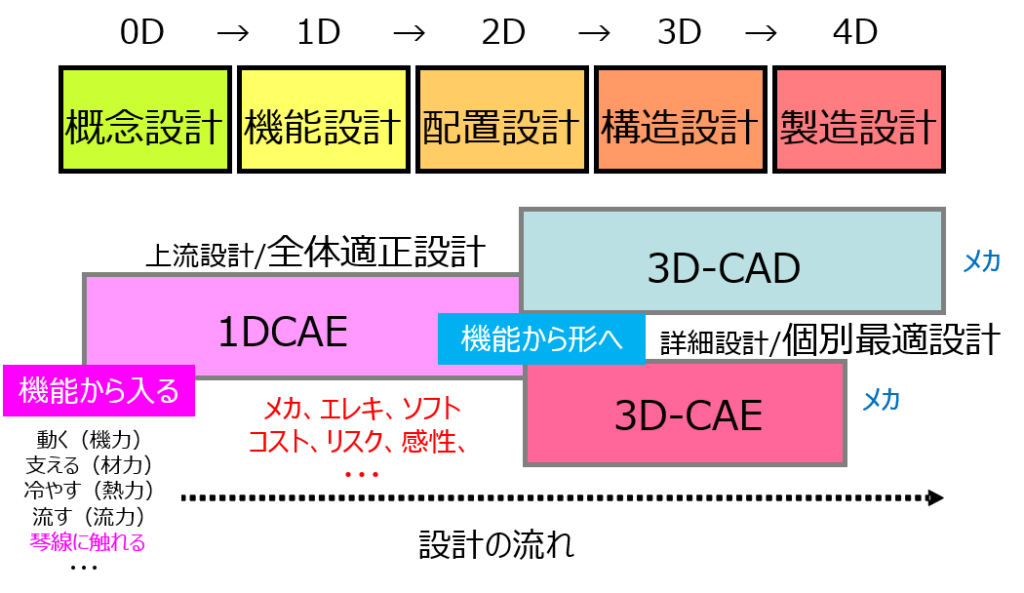
概要
1DCAEと物理モデルシミュレーション
1DCAEが目指すところをそのまま具体化するツールはまだ存在しません。しかしながら、物理モデルシミュレーションは1DCAEの考え方を具現化してくれる一つのツールとして有力です。一例として、物理モデルシミュレーションを用いた1DCAEによる稼働ステージの設計イメージを示します。稼働ステージは稼働テーブル、これを駆動するモータ、機構、モータを駆動する制御(ソフト)からなっています。これを1DCAEの一つの姿である物理モデルシミュレーションで表現すると右下のようになる。この段階ではメカ部部分の形状は気にしなくてよく、質量、バネ定数といった離散情報だけが必要です。この1DCAEで最適な質量、バネ定数を決定し、これを実現するように左上の3D-CAD/CAEを用いて形にしていきます。ここで決定された詳細情報から最終的な質量、バネ定数を1DCAEに戻し、稼働ステージとしての機能を検証します。
非常に簡単な例ですので1DCAEの効果が理解できないかもしれませんが、実際には複雑なシステムにも適用可能です。ただ、現状の物理モデルシミュレーションツールはすべての物理現象を扱えるわけではなく、1DCAEが目指すコンセプトの実現にあたってはさらなる改良もしくは別の全く違うコンセプトのツールが必要となる可能性があります。
実は1DCAEは特殊な考え方ではりません。昔から、技術者は対象としている製品をモデル化したいと考え、自分の能力の範囲で時間をかけてモデル化、パラメータサーベイをしていました。しかしながら、最近は製品開発のサイクルが短くなり、このようなことでは間に合わなくなりました。また、(狭義の)CAEの普及で開発効率は上がったものの、技術者の思考がワンパターン化し、価値ある製品の創出にブレーキがかかってしまいました。1DCAEはこのような現状の課題に対して、一つの解を示してくれる可能性のある考え方、手法、ツールです。物理的なことを理解していれば1DCAEを用いて短時間で対象製品をモデル化することが可能です。ここで目指す1DCAEは上記の機能も有しながらより広範囲により柔軟に設計を支援する概念です。
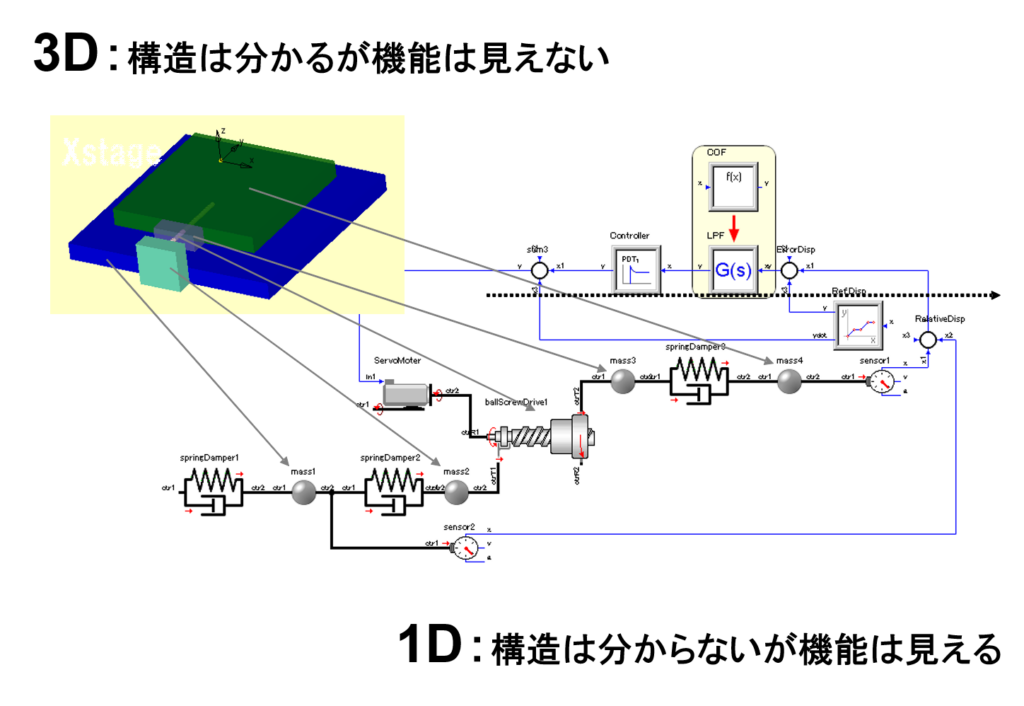
1DCAEの効果
1DCAEのものづくりの視点から重要な効果は上流設計の実現とシステム全体の可視化、エンジニアの育成とこれによりもたらされるものづくりの革新です。
上流設計の実現: 設計上流段階から適用可能なため、広い設計空間を対象とすることができ、結果として新たな価値の創造につながります。また、設計の早い段階で設計の問題点を見つけることができ、結果として設計の質の向上、効率向上につながります。従来の3D-CAE手法は部分最適を可能としていたものの、システム全体を見通した全体最適は不得手でした。1DCAEは全体最適による価値最大化、コスト最小化、リスク最小化を可能とします。
システム全体の可視化:メカ、エレキ、ソフトといった分野を横断した設計仕様の策定が可能となります。これは分野単独の部分最適から、分野横断の全体最適を可能とし、ムリ、ムダを排除できます。また、システム全体での抜けを防止でき、品質向上につながります(安心安全の実現)。また、結果の可視化だけでなく、メカ、エレキ、制御といった機能の可視化、機能を実現するパラメータ(数値)の可視化、どの分野を対象としているのかといった情報の可視化を実現します。
エンジニアの育成:1DCAEはエンジニアの思考を容易に計算機上に具現化してくれます。しかし、これはエンジニアの資質に大きく影響します。1DCAEではこれが3D-CAE以上に如実に表れます。すなわち、1DCAEは物理現象をちゃんと理解していることにより最大の効果を発揮し、考えている対象製品イメージを機能に展開する能力が要求されます。当然、システム全体を対象としているので自分の専門分野以外のことも知る必要があります。例えば、機械屋だったらモータのことも勉強しないといけないかもしれません。このように、1DCAEはエンジニアに学習を能動的に働きかける重要な効果があります。
1DCAEの適用プロセス
1DCAEは設計の目的によって構成が大きく異なる。目的に応じて設計を3つに分類します。3つの設計は狩野モデルを基本にMust設計、Better設計、Delight設計に分類できます。
Ⅰ. Must設計(“あたりまえ品質”に相当):デザイン保証が必須の設計。多くのトラブルはこの設計をないがしろにすることによって発生します。評価されにくいため取組みにくい領域するが設計の基本です。リスクの最小化が目的となります。
Ⅱ. Better設計(“性能品質”に相当):評価が明白なために取り組みやすい領域ですが最終的にはコスト競争に陥ります。コスト最小化、開発期間最短化、性能最大化が目的となります。
Ⅲ. Delight設計(“魅力品質”に相当):デザインコンセプトが最重要となる設計です。多くのヒット商品はこの領域から生まれます。創発的な設計と思われがちですが、技術、顧客要求の先取りがポイントとなります。例えば、心地よさ最大化が目的となります。
3つの設計を念頭に置いた1DCAEの製品設計への適用プロセスを図に示します。製品開発においては社会動向、顧客ニーズ、自社の強み等を考慮して目標を設定します。これを受けて設計が開始します。概念設計、機能設計においては1DCAEの考え方に基づいて全体適正設計の枠組みの構築、評価を実施します。この部分は3つの設計によって内容が異なります。1DCAEで決定された仕様は3D-CAE(個別設計)に受け渡され、メカ、エレキ、ソフト、意匠設計を実行、個別V&V(Verification & Validation)が行われます。個別設計の結果は1DCAEに戻され、システムV&Vを行い、システムおよび個別の成立性を確認した後に、製品製造へと受け継がれます。1DCAEという全体適正設計の枠組みを設定することにより、新たな気付きを誘発、結果としてものづくりの革新をもたらすことを想定しています。
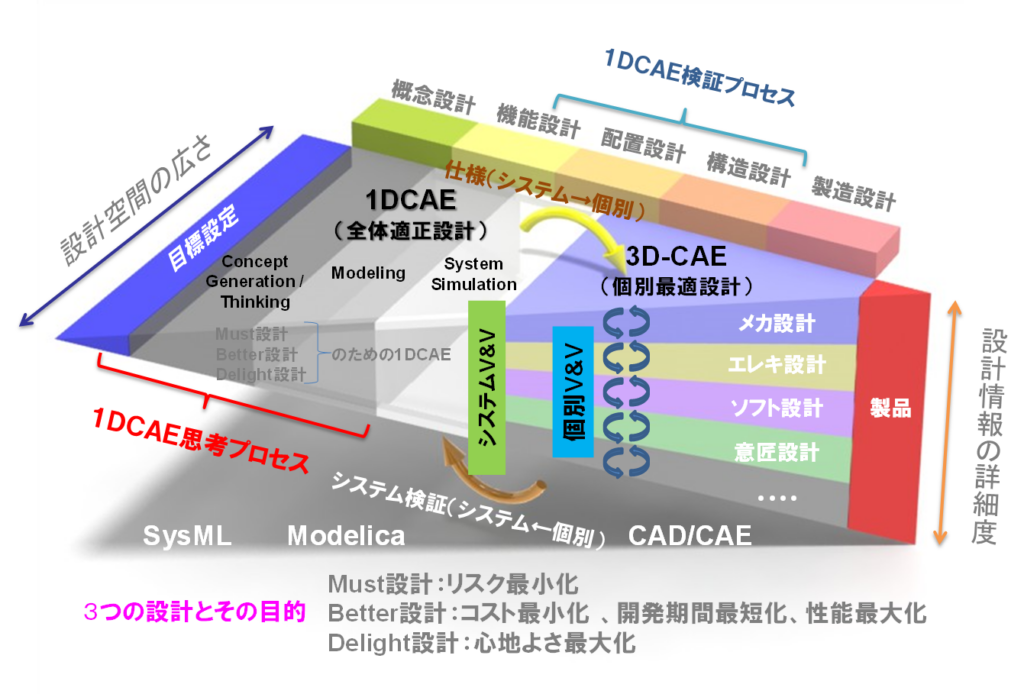
事例等
Better設計と1DCAE
医用機器を対象としたBetter設計(コスト最小化)における1DCAEの適用例を示します。
構造物の軽量化を実現することによりコスト削減を狙ったものです。3D-CAE/CADを基本とした従来手法により、形状最適化により大幅な重量削減は可能となりましたが、コスト削減効果は10%以下でした。自動車、モバイル機器の場合には軽量化が燃費向上、携帯性向上といったコスト削減以上の価値に結び付きますが、この例では軽量化が製品価値向
そこで単なる重量削減等によるコスト削減でない本質的なコスト低減を目的に1DCAEの適用を行いました。図にその適用プロセスを示します。1DCAE部分では市場・顧客分析により顧客要求を抽出、さらに機能から構造に展開します。この部分で本質的なコスト低減のアイデアを複数創出します。創出された複数のアイデアに対して機能設計を実施、性能予測(メカ・エレキ・ソフト統合解析)を実施、同時にコスト予測も行うことによって、設計上流での性能、コストトレードオフ問題に導きました。ここで得られた複数の案から性能/コスト比の高い案を選定、その製品仕様をもとに詳細設計/個別設計へと展開しました。この1DCAEの考え方、手法により従来の設計法では得られなかった新しいコンセプトも生まれました。1DCAEを適用することにより、40%を超えるコスト削減を実現しました。具体的には性能を維持改善した上でコスト削減が可能な駆動方法の採用、モータ等のコストの高い要素部品の限界設計が大幅なコスト削減に寄与しました。これらは3D-CAE/CADによる詳細設計段階では実現できなかったものです。
アイデア創出部分について説明します。機能に対応した構造を網羅的に抽出し、実現可能性も考慮して大幅なコスト削減が可能なアイデアを抽出しました。この際、設計の基本、製造の基本といったノウハウ、過去の知見を参照するとともに、設計論の考え方も加味した機能の構造への展開を経て幾つかの設計案を創出しました。1Dでは設計案の性能をシステムシミュレーション(メカ・エレキ・ソフト統合解析)で予測、速度ムラ等が規定値内で収まっていることを確認、あわせてコスト削減効果も確認します。1Dで決定した質量、ばね定数、減衰係数等の基本情報をもとに、3Dで形状設計、性能設計(変位、応力)、製造設計を実施、最終的に求めた形状情報を1Dに縮退して1Dに戻し、要求仕様を満足していることを確認します。
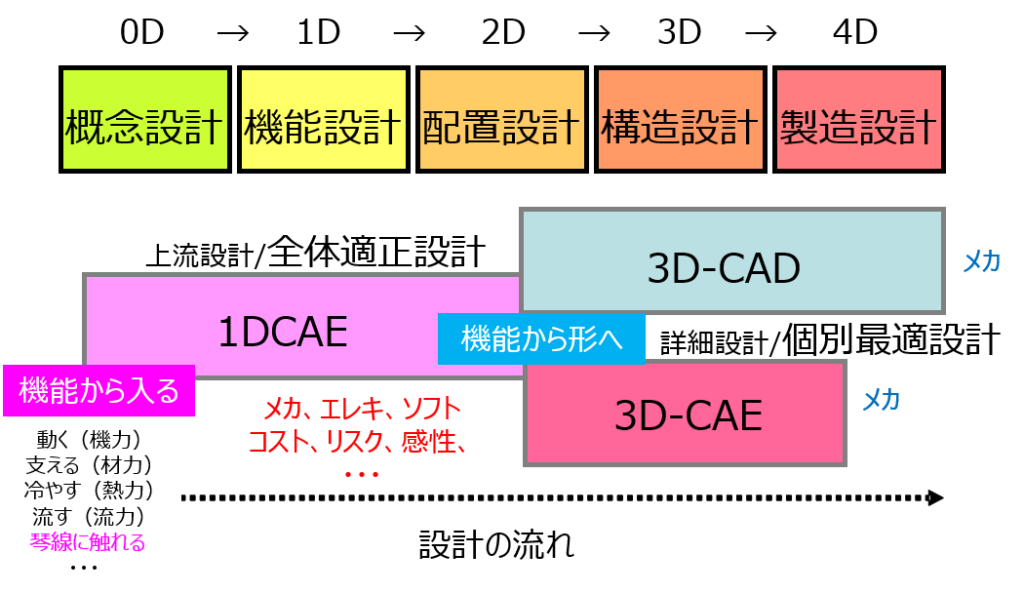
Must設計と1DCAE
Must設計の目的はリスクを予測し、事前に対策をとることにあります。従来のリスク評価は機能・構造マップを作成し、ある機能が作用しなかった場合にリスクがどのように伝播するかを人間系で行っていました。この方法だと実施する人によるばらつき、抜けが生じる可能性があります。
一方、1DCAEでは各機能、各構造の関係がシステムシミュレーションモデルとして計算機が理解可能です。この性質を利用してMust設計、すなわち、リスク解析の自動化が可能となります。この場合、各要素のリスク表およびイベントは設計者が定義する必要がありますので、現象をちゃんと理解しておく必要があるのは言うまでもありません。
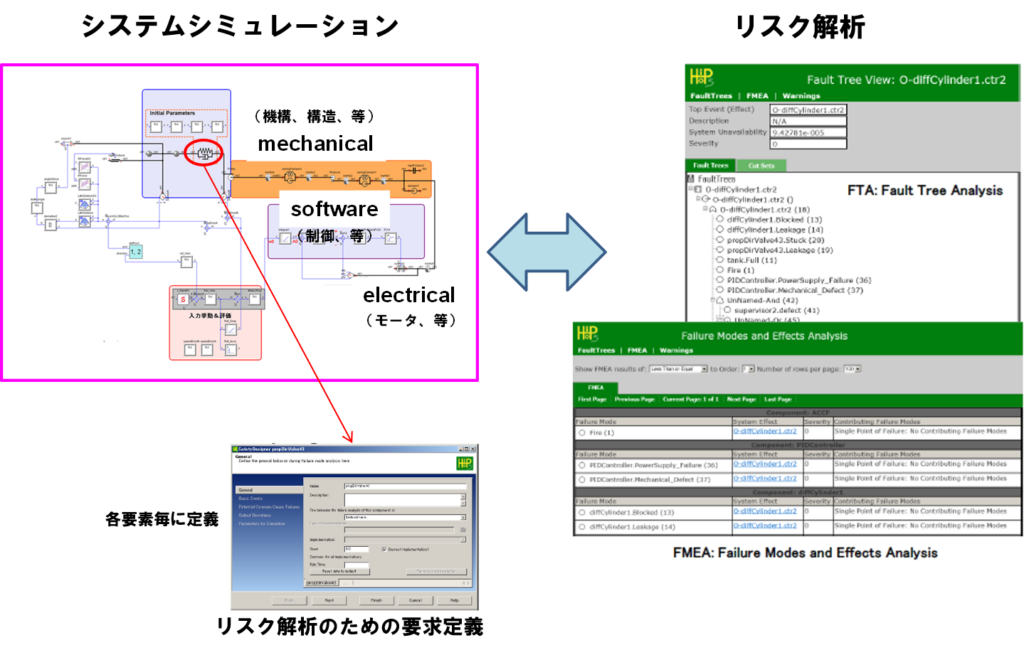
Delight設計と1DCAE
家電機器を対象としたDelight設計(心地よさ最大化)における1DCAEの適用例について説明します。従来、製品が発する音は騒音と呼ばれ、その大きさを低減することに注力していました。この流れは現在も続いていますが、ここでは視点を変えて音を製品の一つの価値として捉える音のデザインなる設計手法を提案しています。音を騒音でなく価値としてとらえるには、音に関する顧客の潜在的ニーズの抽出が必要です。顧客のニーズは多様ですので、これを考慮した顧客設定が重要です。一方、騒音の場合は騒音レベルという確立した設計指標が存在します。音を価値と考える場合には、心地よい音を設計者が理解可能な指標に落とし込み、目標とすべき音を設定する必要があります。この顧客ニーズの抽出、音のものさしの策定、目標音の設定がDelight設計における1DCAEです。1DCAEで得られた仕様(音のものさし上の目標音)に基づいて製品設計を実施、試作品の音を音のものさしにマッピングして性能検証を行い、最終的に目標を満足する音質を有する製品開発が実現できました。具体的にはモータをばね支持構造(従来はモータを吸音材で囲んでいた)するという簡単な構造で心地よい音を実現した。1DCAEに基づくDelight設計を適用しなければこのような構造は生まれませんでした。このDelight設計は製品開発の初期段階からBetter設計、Must設計と一体で実施したため、心地よい音を実現するための新たなコストの発生、性能への影響もありませんでした。
Delight設計は人の感性を扱うことになります。人の感性も機能の一つですが、Better設計、Must設計で対象とする機能のように直接構造に対応させることが困難です。そこで、機能と構造を音質指標という接続媒体を介して結合しています。音質指標は音響心理学の分野の成果として生み出されたもので、人の音に関する感じ方を客観的な数値(音データを分析処理したもの)として表現したものです。Loudness(音の大きさ)、Sharpness(音の甲高さ)、Roughness(音の粗さ感)、Fluctuation Strength(音の変動感)が代表的な音質指標としてよく使用されています。これにより、“心地よい”と言った感性情報を客観的な数値で表現することを可能としました。このようにして導出した指標をここでは“音のものさし”と呼んでいます。人の感じ方(官能試験)と音質指標という客観情報を統計的に処理することにより、官能指標(心地よさ)を音質指標の関数として定義しています。
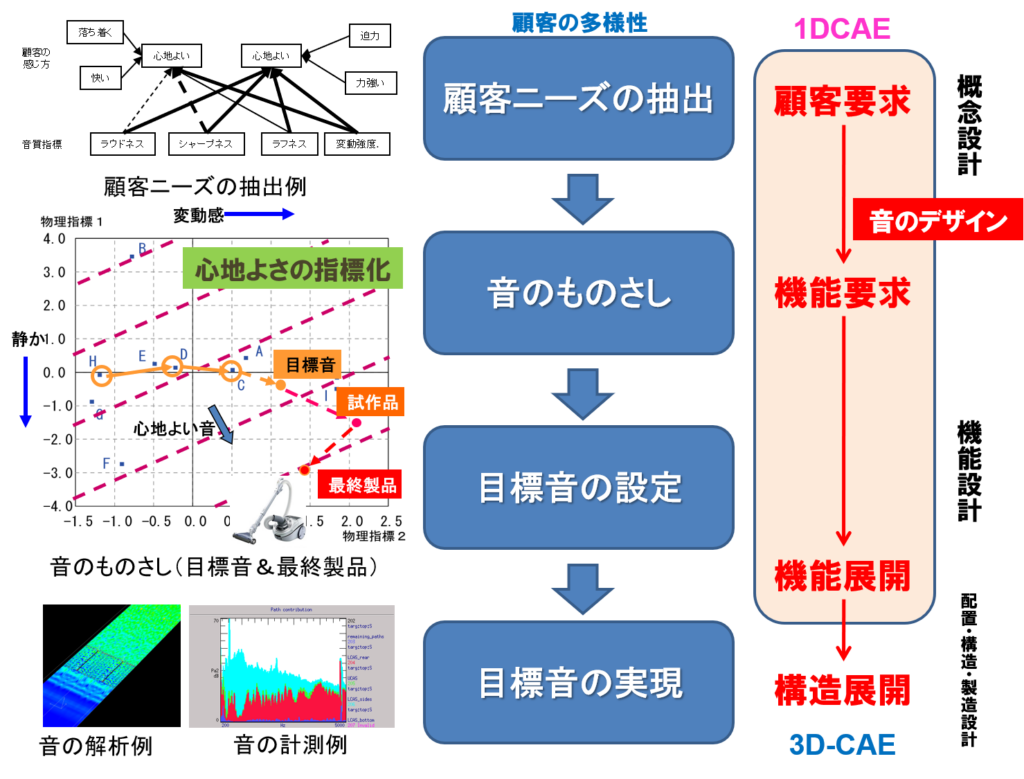
1DCAEの実行イメージ
最初に設計の定義について考えてみたいと思います。Ashbyによると設計はFunctionality→Usability→Satisfactionを形成するプロセスとあります。ここで、Functionality+UsabilityはBetter設計+Must設計に相当し、SatisfactionはDelight設計に相当します。ここで重要なことは、Delight設計はBetter設計、Must設計の上に成り立っているということです。すなわち、Delight設計を行うということは同時にBetter設計、Must設計も行っているのです。
1DCAEを実行するにあたってはBetter設計、Must設計、Delight設計のモデルイメージを明確にしておく必要です。図に家電機器を例とした3つの設計の関係を示します。機能は3つの設計でこのように比較的明確に分けることができますが、構造は実際には一つの構造が3つの設計の機能に関係する場合も多いです。
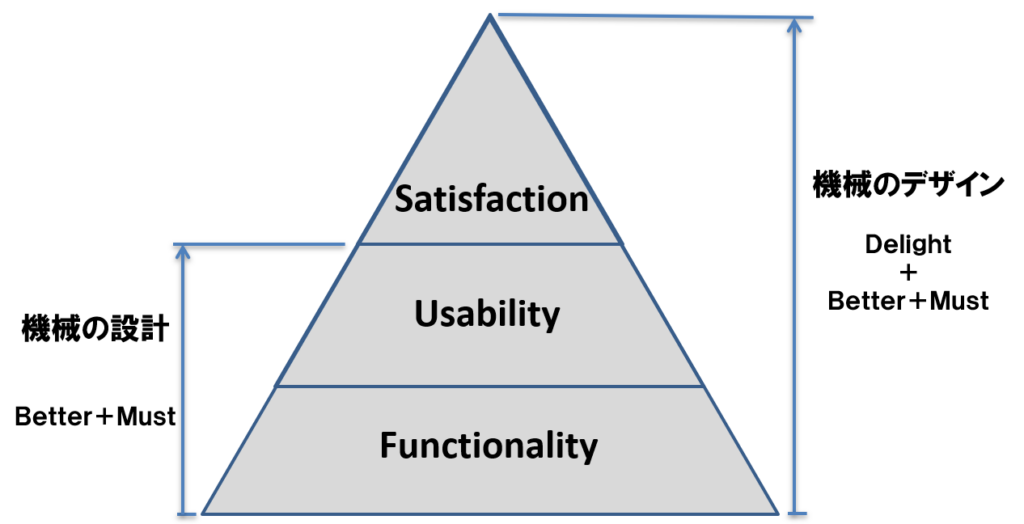
図に1DCAEの実行イメージを示します。Better設計→Must設計の手順を示します。まず、機能・構造マップを基本に設計アイデアの抽出を行います。この結果として、構造が具体化、要素の定義が行われます。次に、製品、構造、要素の情報から物理モデルを構築します。物理モデルには性能、コスト、リスク、感性等に関するあらゆる情報が含まれます。例えば、性能を対象としたBetter設計では物理モデルから性能モデルを構築、性能解析を行います。リスク予測を目的としたMust設計では要素のリスクデータ(リスクDB)と機能から定義されるイベント定義、故障率定義を物理モデルに参照させることにより、リスクモデルを構築、リスク解析を行います。同様にDelight設計では図に示すように、要素のデライト表(感性DB)と機能レベルのデライト定義情報を物理モデルに参照させることにより、感性モデルを構築、デライト解析を行います。
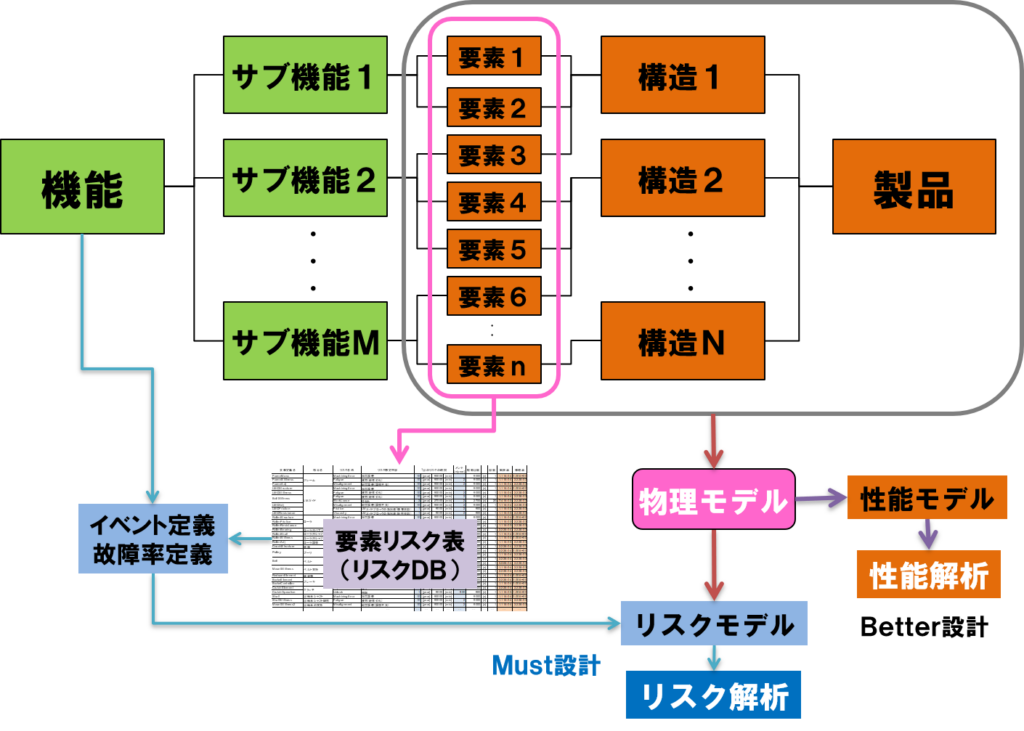
1DCAEで用いる設計手法
設計は英語でDesignです。Designは日本語ではデザインまたは設計です。しかしながら、デザインと設計では受ける印象がかなり異なります。日本でデザインというと意匠設計(Industrial Design)という狭い範囲にとられることが多く、一般には設計という言葉を使うことが多いですが、設計も作図(Drafting)のイメージが拭い切れません。そこで設計を3つの視点で分類し、これに設計手法をマッピングしたいと思います。
最初に設計を開発プロセス(手順)の視点で考えます。製品にもよりますが新製品の開発を想定した場合、最初にだれを顧客としてどのような製品を幾ら位でいつ頃までに開発するのかを考えます。このプロセスは企画と言ったり構想設計と言ったりしますがここでは“概念設計”と呼ぶことにします。製品開発の方向性が概念設計によって仮決めされると次に具体的にどのような機能をその製品に盛り込むかを検討する“機能設計”に移行します。機能設計の段階で機能を実現する部品、材料、構造のイメージも同時に検討します。これを受けて、ものとしての成立性を検討する“配置設計”を行います。レイアウト設計と言ったりもします。決められたスペースに空間的に収まるかが一次的に検討されます。できれば、この段階で空間の影響を強く受ける熱、音の問題を検討しておくことが望ましいです。次に、強度、変形といった構造としての成立性の検討を行う“構造設計”となります。そして、最後に製品をどのように生産するのかを検討する“生産設計”となります。以上から、開発プロセスの視点からは
概念設計→機能設計→配置設計→構造設計→生産設計
となります。一般にはこのようにシリーズに設計が進行しますが、DfXのように製品開発の早い段階でコンカレントに各設計の検討を始めておくことが、後戻りをなくす意味からも重要です。
次に設計行為の視点から考えます。設計行為とは何をしているのかということで、ここでは設計行為を
発想、分析、評価、可視化
の4つに分けます。この4つに時系列的なものは存在しませんが、大まかには発想して、分析して、評価して、最後に可視化する場合が多いと思います。例えば、形状を考える場合には頭で発想して、形状の成立性(含む、干渉チェック)および可視化をCADで行います。性能を考える場合には分析をハンドブック等で行い(中り計算)、形状が見えてきた段階で評価および可視化をCAEで行います。
もう一つの視点が設計目的です。設計目的とはその設計の成果として何を得られるのかということです。ここでは設計目的を
創成、定義、実現、生産
の4つに分けます。この場合は、概ね時系列として、創成→定義→実現→生産となります。“創成”とはどのような製品を創出したいのかを考え、その結果として製品のイメージを第三者が理解できる形で示すのが目的です。“定義”は創出された製品イメージを設計可能な形式で定義します。いわゆる仕様書がこれに相当します。“実現”では定義された製品仕様に基づいて1DCAEの考え方で1D→3D→プロトタイプと製品イメージを具現化します。“生産”では材料、プロセス、体制、環境負荷等を具体化します。
以上、3つの視点から分類した設計手法を一つの絵にすると図のようになります。さらに、この図から分かるように1DCAEは設計の中核をなし、コンセプトを実体に繋ぐ重要な役割を担っています。
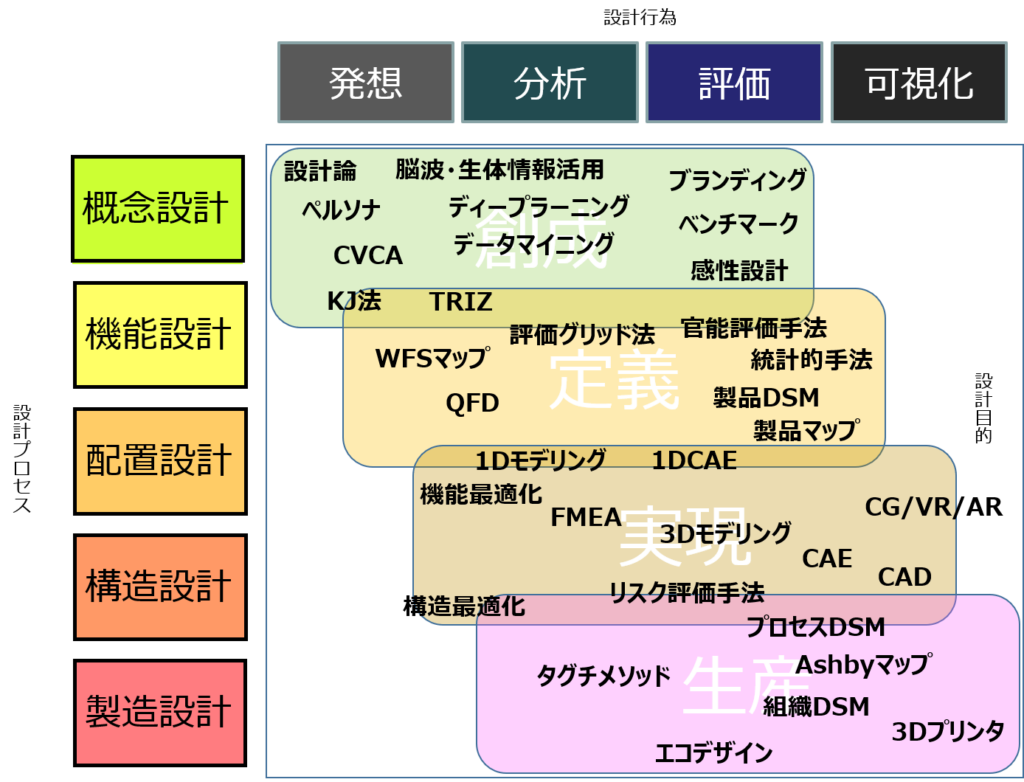
DfXという製品開発の考え方
DfX (Design for X) という言葉を始めて使ったのは1990年、米国Bell研のFooらと言われています。競争力と利益を生む製品開発のための考え方としてDfXを提唱、あわせてその具体的方法も示しています。製造、流通、据付、運転、サービス、保守を設計段階で十分に考慮して製品ライフサイクルを通しての性能および利益の最大化を目的としています。従来、トップダウン的であった米国の製品開発においても、日本との競争に打ち勝つためには、さらに、戦略性が必要であるとして、DfXの概念を考え、実践したことは興味深いです。その後、DfXはDfP(生産性設計)、DfA(組立性設計)など主に製造性に重点をおいたDfX、すなわち、DfM (Design for Manufacturing) を中心に展開されてきました。一方、1990年代後半になると時代を反映して、環境負荷を考慮した製品開発、顧客主導型製品開発といった従来にない新しい設計法が必要となってきました。
そこで、ここではDfXをFooが最初に定義した考え方に基づき、さらに環境負荷、顧客の声をも含めた、より広く製品ライフサイクルを通して製品価値の最大化を設計段階で図る考え方およびそのための手法と定義したのがスタンフォード大学の石井先生です。
製品開発プロセスは一般に図のようになっています。製品イメージを検討する企画構想(コンセプト設計)、企画での仕様に基づいて製品イメージを具体化する概念設計、さらにより詳細な設計、部品、材料等の調達、製造/組立を経て製品として完成します。製品は出荷、据付/調整され、稼動状態となります。稼動後もサービス/メンテナンスにより常に最適な状態で稼動できる状態を保つ必要があります。寿命を全うした製品は一部廃棄、一部回収再生され、さらに新規製品開発に供されます。このように、製品開発はライフサイクルを描いています。
製品開発のライフサイクルコストは製品開発の進行とともに図のように決まっていきます。すなわち、設計終了段階で製品の全ライフサイクルコストの80%が確定します。これは試作調達、製造組立以降の変更は大きな後戻り(バックトラック)を発生し、製品開発にコスト、スケジュールの両面で甚大な影響を与えることを意味します。したがって、設計を戦略的かつ効率的に実施し、それ以降の製品開発での後戻りを減少させることが製品開発において非常に重要であることが分かります。設計でも、詳細設計となると作業的にも負荷が大きくなり、設計のやり直しは製品開発全体に少なからぬ影響を与えるため、できればより上流の概念設計段階で可能な限り種々の側面からの検討を行なうことが重要です。
上流設計を具体化するための考え方DfX
上流設計を具体的に実施する考え方としてデザイン・フォー・エックス(DfX)があります。DfXは製品のライフサイクルを通して発生すると想定される諸問題を、企画、概念設計(上流設計)段階で検討することによって、詳細設計以降の製品開発後半での後戻りを極力減らす考え方です。スタンフォード大学の石井教授の定義によると、『DfXとは、製品開発において企画から設計に移行する際、論理的にプロジェクトの性質を解析し、それにふまえて焦点をさだめ、以降の開発活動に有効な個々の設計手法(DfXのX)を選択し投入計画を立てる活動である』とあります。
図にDfXの概念図を示します。性能検証のための設計だけでなく、製造性、組立性、保守性を考慮した設計、環境に関わる解体性、リサイクル方法を考慮した設計、さらには使いやすい、飽きがこないといった顧客要求満足度に関する項目も評価対象となります。DfXのXは評価する項目を意味します。例えば、製造性(Manufacturing)評価のための設計はDfM、環境(Environment) 評価のための設計はDfEなどといった具合です。
DfXは製品によってもアプローチの仕方が異なります。ある製品(Y)に関するものを、DfX of Yと呼ぶことがあります。例えば、ノートPC開発では、性能面では冷却を考慮した設計、環境面では廃却/リサイクルの容易な材料選定および解体のし易さを考慮した設計法が必要となります。一方、宇宙機器の場合には、極力トラブルが発生しない設計、また不幸にして発生しても対応できる仕組み、構造を考慮した設計が必須となります。DfXは製品開発の考え方、総称です。この実現のためには多くの設計手法を用います。DfXという考え方の元、具体的な製品に対してこれらの手法、ツールを如何に組み合わせて効果的に活用するかがポイントです。
DfXを具現化するには、個別の設計手法が必要となります。CAD,CAM,CAE,PDMといった従来型製品開発手法と、QFD,FMEA, DSMといった今まで設計とは違った目的で使用されていた手法を、DfXという一つの考え方の元、共通的に扱うことによって大きな効果が期待できます。実際には、設計の過程、目的とする製品ライフサイクルの項目に応じて最適な手法を適用します
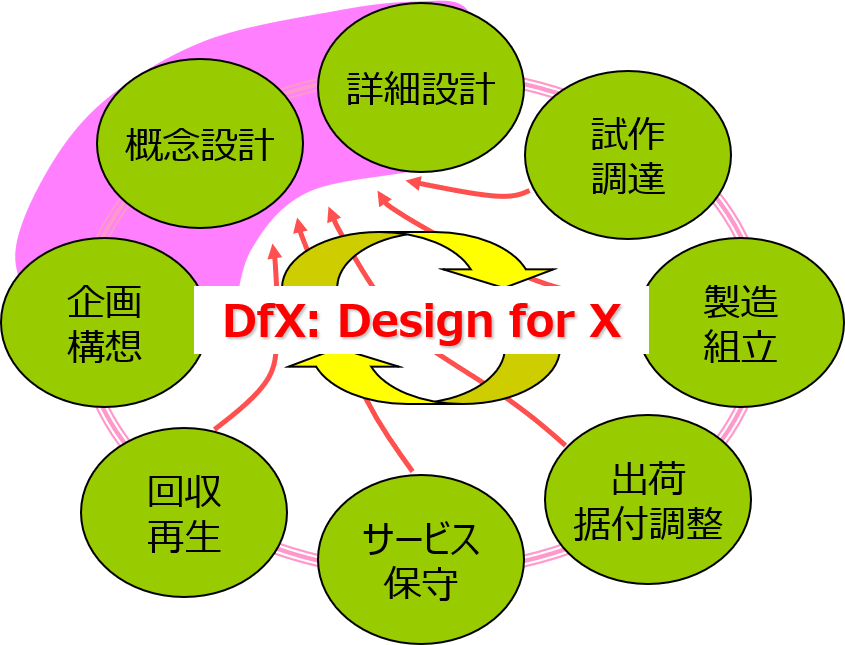
DfXを具現化する手法:その1(QFD)
顧客の声を抽出し、定量化し、設計に結びつける手法がQFDです。QFDは品質(Quality)機能(Function)展開(Deployment)の略で、顧客の声を製品開発の意思決定に反映することを目的としています。企画段階で顧客の声は測定可能な機能と関連付けられます。さらに、設計段階で、機能は部品に関連付けられます。このプロセスを経て、顧客要求度から見た部品の重要度を評価できます。同様に、生産管理、製造へと顧客の声が反映されます。従来は曖昧であった顧客の声を価値で示すことによって、製品ライフサイクルを通して顧客要求を正確に伝えることが出来ます。
図にQFDの適用例を示します。STEP1:企画では、顧客の声と機能の関連付けを行います。ここでは、お互いに関連が深い項目を◎、関連がある項目を○、関連が若干ある項目を△で表記しています。これ以外にも数値で表現する場合もあります。また、顧客の声の重要度は一様ではないので重み付けを行っています。STEP1から各機能の優先順位が定量的に把握できます。次に、STEP2:設計では機能と部品の関連付けをSTEP2と同様にして行います。以下、STEP3:生産管理で部品と製造方法の関連付けを行います。さらに、出荷、組立調整、サービス、保守、回収、再生と展開することも可能で、最終的には再生から顧客の声へと戻ります。このように、QFDの利点は顧客の声を製品開発の各フェーズの意思決定に反映できる点にあります。
QFDを実際に使用する際の問題は顧客の声、機能、部品の各項目をどのように選ぶかです。これに対しては確たる方法があるわけではなく、基本的には設計者の技量に任されています。一つの方法を図に示します。ここでは顧客の声を起点に、機能、部品との関連付けをマップ上に表記しています。これにより、自由に項目の選定が行えるとともに、お互いの関連付けも試行錯誤で行うことができます。ここで部品とはハードウェアだけでなく、ソフトウェア、サービス、等も含むことに注目する必要があります。
QFDは手法としての単純さから、多くの設計者が使った経験があると思いますが、その効果に対して疑問を抱く設計者も多いのではないでしょうか。QFD自身が目新しい解を提示してくれるわけではなく、自分の頭の中を整理する手法、プロジェクトメンバー間での情報の可視化手法と考えるべきです。設計プロセスがQFDを通して明らかになることによって、設計者の判断を効率的、かつ、正確に行うことができます。
一方、QFDでは最初の段階で”顧客はだれか”を明確にする必要があります。この際、有効なのが図に示すCVCA (Customer Value Chain Analysis) であす。QFDとセットで是非使用していただきたいと思います。
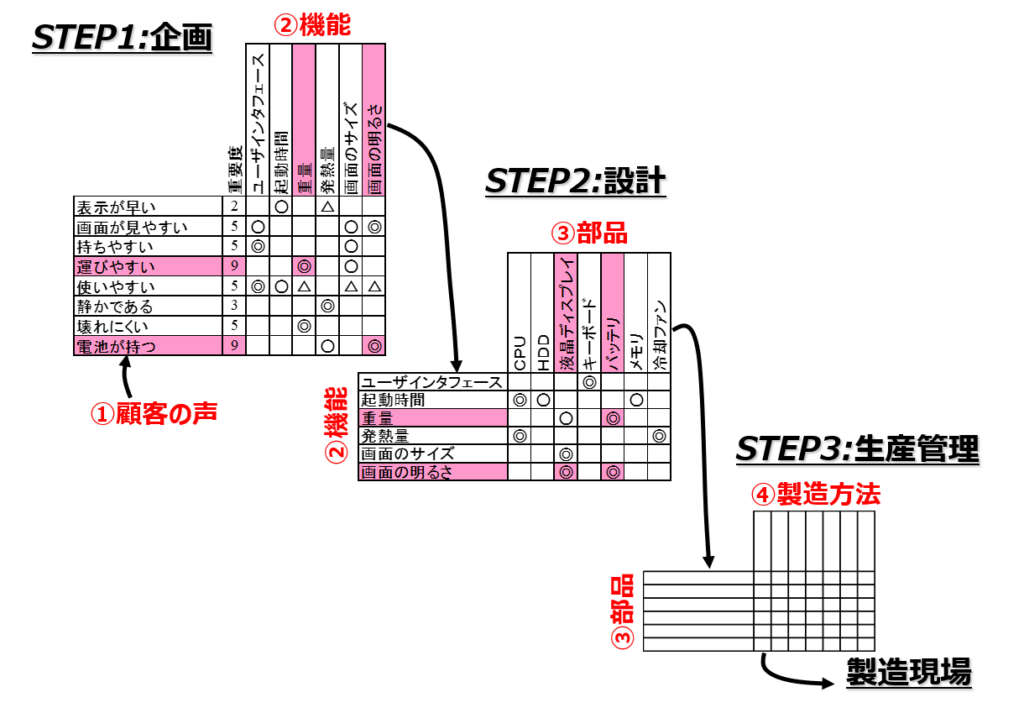
DfXを具現化する手法:その2(FMEA)
FMEAはもともと、設計や工程計画の構想段階で、起こるであろう問題の原因を事前に予測して、問題を未然に防止する管理手法で、故障モード影響解析と訳されています。ここでは、製品開発の各段階で発生が予測されるリスクを抽出、定量化し、対策後のリスク低減を確認する手法としてFMEAを考えます。
FMEAには3つの機能があります。
(1)何が悪いのか、
(2)何が原因か、
(3)どうしたら改善できるのか
の3つです。FMEAの手順を図に示します。まず、故障モード、原因、影響を特定します。次に、発生頻度(O)、発生した場合の深刻度(S)、予測困難度(D)の積でリスクを定量化します(場合に応じて、これら3項目の内、1項目ないしは2項目を用いる場合もあります)。高いリスク項目に関して、設計/プロセスの改善を行い、改善後のリスクを定量化し、十分にリスクが低減してことを確認します。
FMEAの適用例を図に示します。FMEAではまず問題点を抽出することから始まります。これはQFDの項目抽出と同様、万能な方法があるわけでなく設計者がどれだけ対象としている設計課題を理解しているかに依存します。問題点抽出の例としては、図のようなマップ、この場合は、機能(Function)と構造(Structure)の関係を表すFSマップが活用できます。抽出された項目ごとに、発生頻度、深刻度、予測困難度を数値化します。
図の例では最大値を10としていますが特にこの値に意味があるわけではなく、適宜定義すればよいのです。発生頻度(O)、深刻度(S)、予測困難度(D)を数値からリスクがRPN=OxSxDで求まります。ここで重要なのはリスクをどこまで許容するか目標値を決めることにあります。この例ではリスクの目標値を500以下としているため、得られたリスク値1000は許容できません。従って、対策を講じる必要があります。対策にあたっては、発生頻度、深刻度、予測困難度の各項目が数値化されているので具体的に検討することができます。そして、対策後のリスクも同様に算出します。対策はリスク値が許容値以下になるまで繰り返します。図の例では一項目のみ示していますが、実際のリスクは複数項目存在するため、各項目に関して同様の手順を行い、総合的にリスクを評価します。
FMEA適用重要な点は発生の予想されるリスクをもれなく抽出することであり、このためには現象論的に対象とする製品を理解するとともに、使用状況の予測等、柔軟な思考が要求されます。
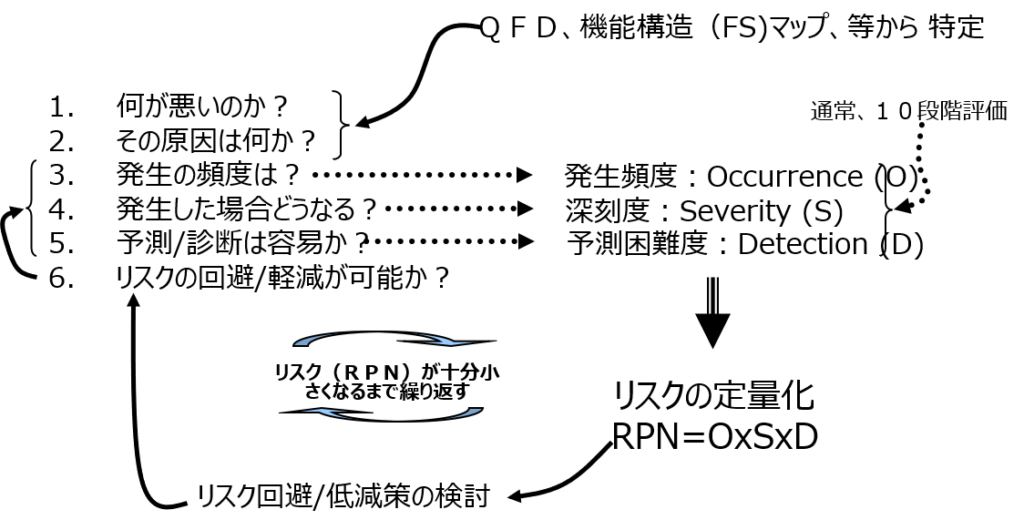
DfXを具現化する手法:その3(DSM)
設計の大規模化、市場への新商品投入のスピードアップ、コスト競争の厳しさなど、製品開発を取り巻く状況の変化に対応するために、全体最適化の視点から、工程や組織を抜本的に改革する必要があります。設計情報の流れを可視化して、効率的な工程、組織をシステマチックに設計する手法として、DSM(Design Structure Matrix)があります。DSMは、マトリクス表現に基づく、工程・組織設計のための手法です。1990年代初め頃から、主に、米国・マサチューセッツ工科大学(MIT)のSteven D. Eppinger教授らを中心として研究され、自動車業界や半導体業界などで徐々に広まってきました。後戻りや反復作業も含めて、複雑なプロセスの構造を簡潔に表現できるという特徴があります。
図に示すようにDSMの縦軸と横軸にはプロジェクトを構成する一連のタスク(作業)が並べられ、マトリクス上のマーク(記号、数字、など)は、タスク間に何らかの依存関係が存在することを示しています。DSM上の(X)はタスク間に依存関係があることを示します。図ではタスクEは、タスクAとタスクBの情報に依存し、タスクC、タスクF、タスクG、タスクHに情報を提供する。DSMの縦軸において、上から下への並び順が、実際にタスクを実行する順番と完全に一致していると仮定します。そのとき、マトリクス上の対角線の下側(下三角部分)にあるマークは、前工程から後工程への情報の流れを示しており、フィードフォーワードと呼ばれる。一方、対角線の上側(上三角部分)にあるマークは、後工程から前工程への逆方向の情報の流れを示しており、フィードバックと呼ばれます。
DSMに基づくプロセス分析の強力な手法として、パーティショニングがある。これは、DSMの上三角部分にあるマークを減らす、または、なるべく対角線に近づけるように、DSMの行および列の順序を入れ替える処理です。図に示すようにパーティショニングを実行した結果、ブロックの大きさは常に最小となることが保証されています。図では、パーティショニング後も、タスクH、タスクJ、タスクMが相互依存関係にあることを示しています。パーティショニングのアルゴリズムには、パス探索による方法、隣接行列のべき乗による方法、グラフ理論による方法など、様々な方法があります。
DSMの基本的機能について述べましたが、その応用範囲は広く、スケジューリング、組織の最適化、製品ライフサイクル設計、等に適用され効果を上げています。ここでは、適用対象に応じて図に示すように製品DSM、プロセスDSM、組織DSMと分類する。製品DSM、プロセスDSM、組織DSMは個別で用いられるだけでなく、図に示すように製品、プロセス、組織を一括して取り扱うDMM(Multi Domain Matrices、マルチドメインマトリックス)へと発展できます。マルチドメインマトリックスは異なる2つ以上の領域のDSMを同時に表現する拡張DSMモデリングで単領域のDSMはMDMの対角線上にあり、非対角ブロックにはDMM があります。DMMはDomain Mapping Matrixの略で、別のDSM の領域へ1つのDSMの領域をマッピングするもので通常は非正方行列となります。
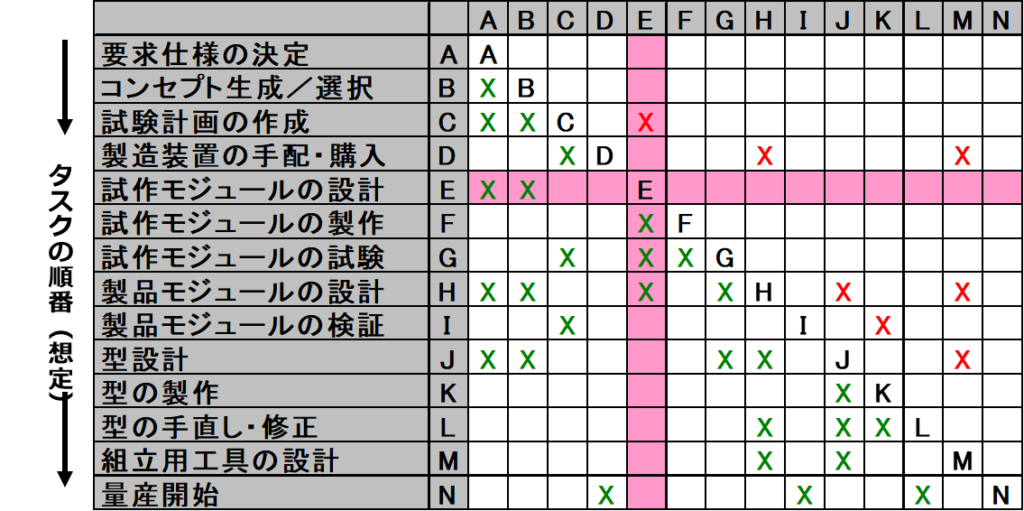